As the heart of the photovoltaic power generation system, solar module is the most expensive equipment and has always been the focus of the whole PV industry. Along with the rapid decline in both cost and price of photovoltaic module, the proportion of module cost in the total cost of photovoltaic system has always been around 50% (slightly decreased). For the cost reduction of the balance of system (BOS) components, on the one hand, it depends on the reduction in the costs of inverter, box transformer and other equipment, as well as the optimization of the array capacity design; on the other hand, it lies in the dilution resulted from the improvement of module efficiency and the change of specifications, which will be analyzed in details as follows.
Improved Module Efficiency Reduces BOS Costs
It’s widely known that efficient modules can reduce BOS costs. Since 2015, the rapid increase of monocrystalline modules and monocrystalline PERC modules in the market share has been recognized due to their advantages in both BOS cost savings and power generation performance. The basic principle for the BOS cost savings is to increase the total power of modules on each bracket by using efficient modules, thus the following items involved in the power station with the same capacity performs approximately proportional decrease:
A.Bracket
B.Combiner box (or string inverter)
C.Photovoltaic cables and DC cables
D.Foundation construction of piles
E.Module and bracket installation costs
F.Initial land cost
For example, in the second half of 2016, a comparison between 60-cell 270Wp polycrystalline module and 60-cell 295Wp monocrystalline PERC module with the same module size shows that the efficiency of the 270Wp module is 8.5% lower. If the BOS costs of polycrystalline module affected by the module efficiency is considered at USD 0.25/Wp, the corresponding BOS costs of the 295Wp module can be roughly calculated based on the efficiency ratio: 0.25*270/295=USD 0.23/Wp, the high-efficiency module brings about USD 0.02/Wp, or about 8.5% in BOS cost savings.
At present, the BOS costs related to module efficiency are lower than those in previous years, but considering the greater decline in module price, the proportion of BOS cost savings in the module price is increased, so the high-efficiency product is more favorable in market.
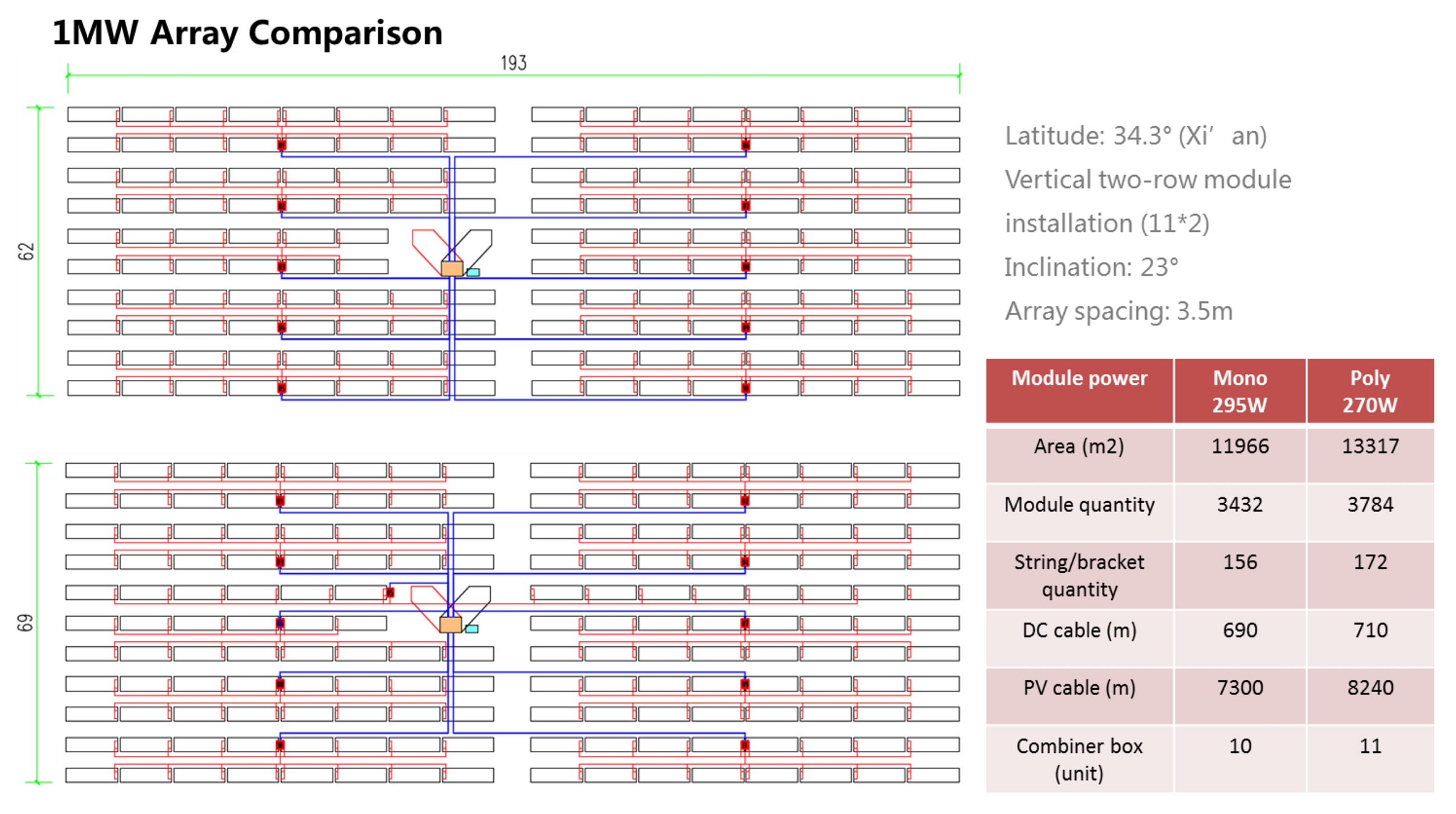
The above calculation takes the same installation capacity into account and is applied to the ground stations with sufficient land. For industrial and commercial roofs (similarly for residential roofs), high-efficiency modules can achieve larger installation capacity, in this way, in addition to the above costs, the following costs can also be diluted by such larger installation capacity, and the use of high-efficiency modules is more profitable:
A.Power station development cost
B.Grid access cost
C.Integrated automation equipment cost
Changes of Module Layout reduces BOS Costs
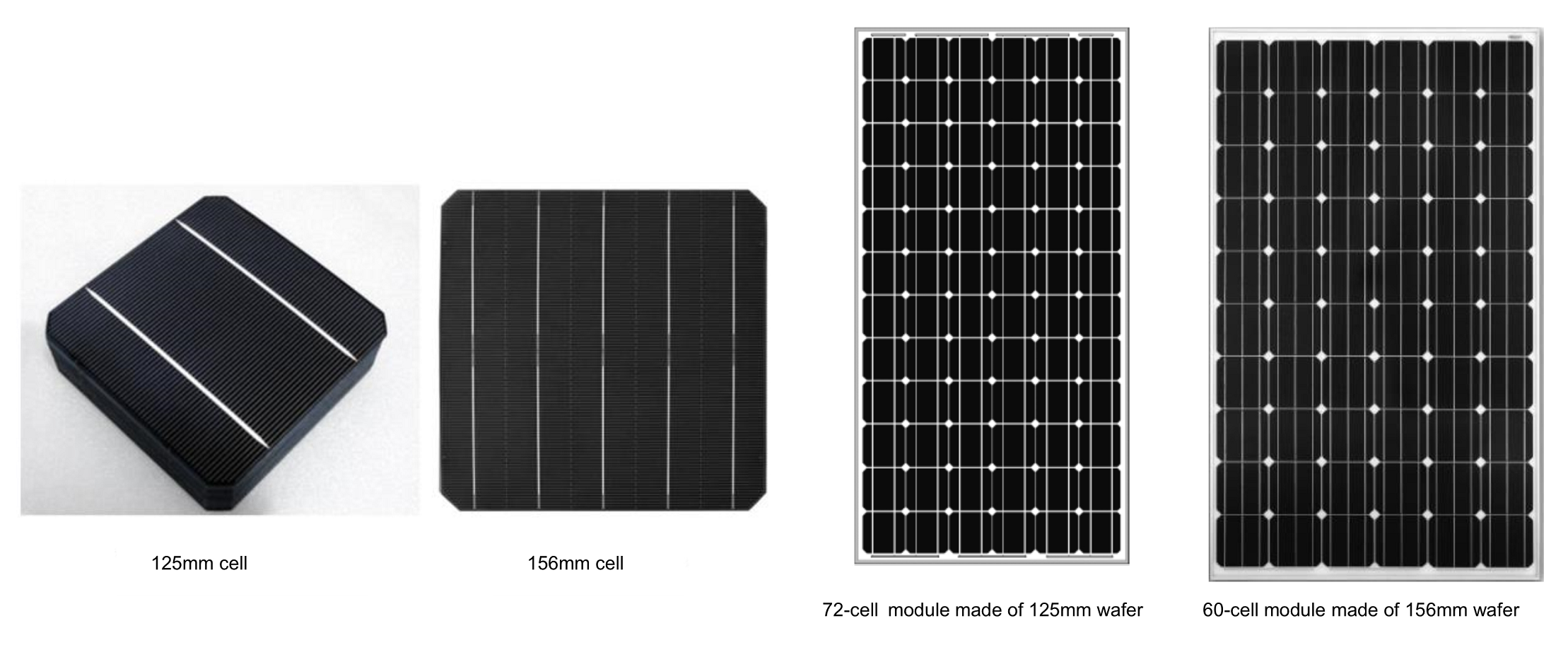
1.Comparison between early module using 125mm cell and module using 156mm cell
In 2012, there were still modules made of 125mm monocrystalline silicon wafers in the market. The size of the modules using 72 cells (6*12) was 1580*808mm, and the power of the monocrystalline module was about 205Wp; at the same time, the power of 156mm 60-cell module was about 260W, and the size was 1650*991mm. The open circuit voltages of these two modules were 45.92V and 38.24V respectively, thus the number of 156mm cell modules in a string was larger. Considering that the power of a 156mm cell module is higher, the total power of a module string is significantly higher than that of a module string using 125mm wafers. Thus, the bracket carrying a string of modules can be made larger, the bracket and foundation costs per Wp can be significantly saved, the labor efficiency on module installation and brackets can be improved due to the power increase of modules, the consumption of PV cables can be reduced, and the land occupation can be slightly reduced.
Such savings cannot be calculated by simple linear conversion, but require the establishment of an array model for specific analysis. The simple calculation results based on the cost model of year 2012 are as follows (the project locates in Golmud and is the same in the rest of this paper), the 30% power increase brings about USD 0.06/Wp or 16% savings in BOS costs related to module power.
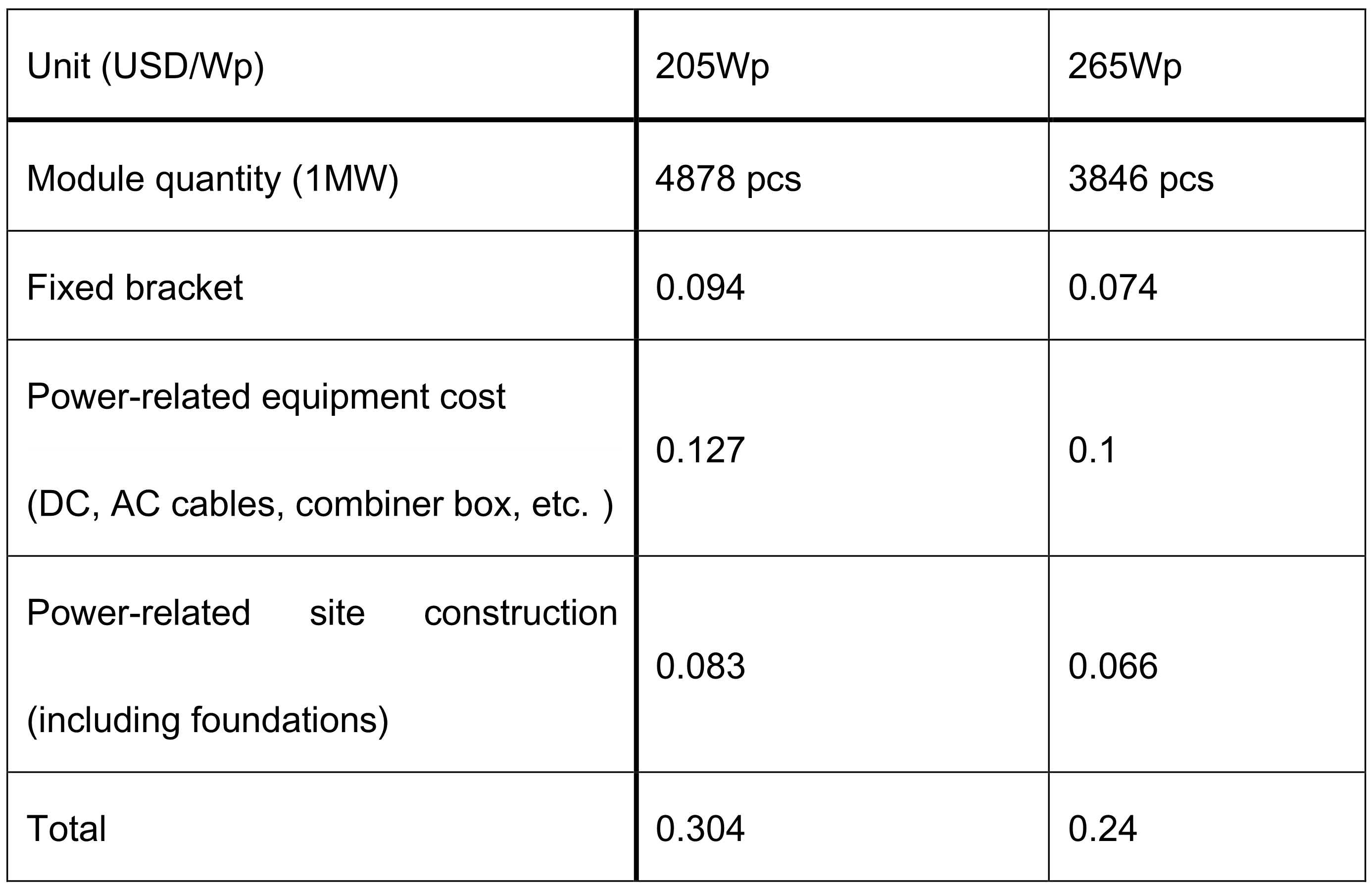
2.Comparison between 60-cell and 72-cell modules
The 156(.75) mm cells can be packed into 72-cell (6*12) module to further increase the power of the module. The increase in the number of cells levels up the open circuit voltage and reduces the number of modules in a string while maintaining the same power level of a single string of modules. However, for the ordinary two-row vertical installation, a slight extension of the oblique beam can make the bracket carry 72-cell modules, and slightly reduce the bracket costs. This effect is more significant when the higher-cost horizontal single-axis tracker is used. Therefore, the horizontal single-axis tracker is usually used together with 72-cell modules; on the other hand, the labor efficiency on module and bracket installation can be reduced due to this increased module power. The preference for 60-cell modules in the Chinese market is mainly a matter of habit. Emerging Asian markets such as South Korea, Southeast Asia and India generally employed 72-cell modules in large power stations and industrial & commercial distributed power stations to reduce system costs.
The following table shows that 72-cell module can bring about USD 0.001/Wp savings in the costs of bracket, cable and combiner box, USD 0.004/Wp savings in the cost of installation simply calculated by following the number of modules, and overall USD 0.006/Wp savings in BOS costs on the system side.
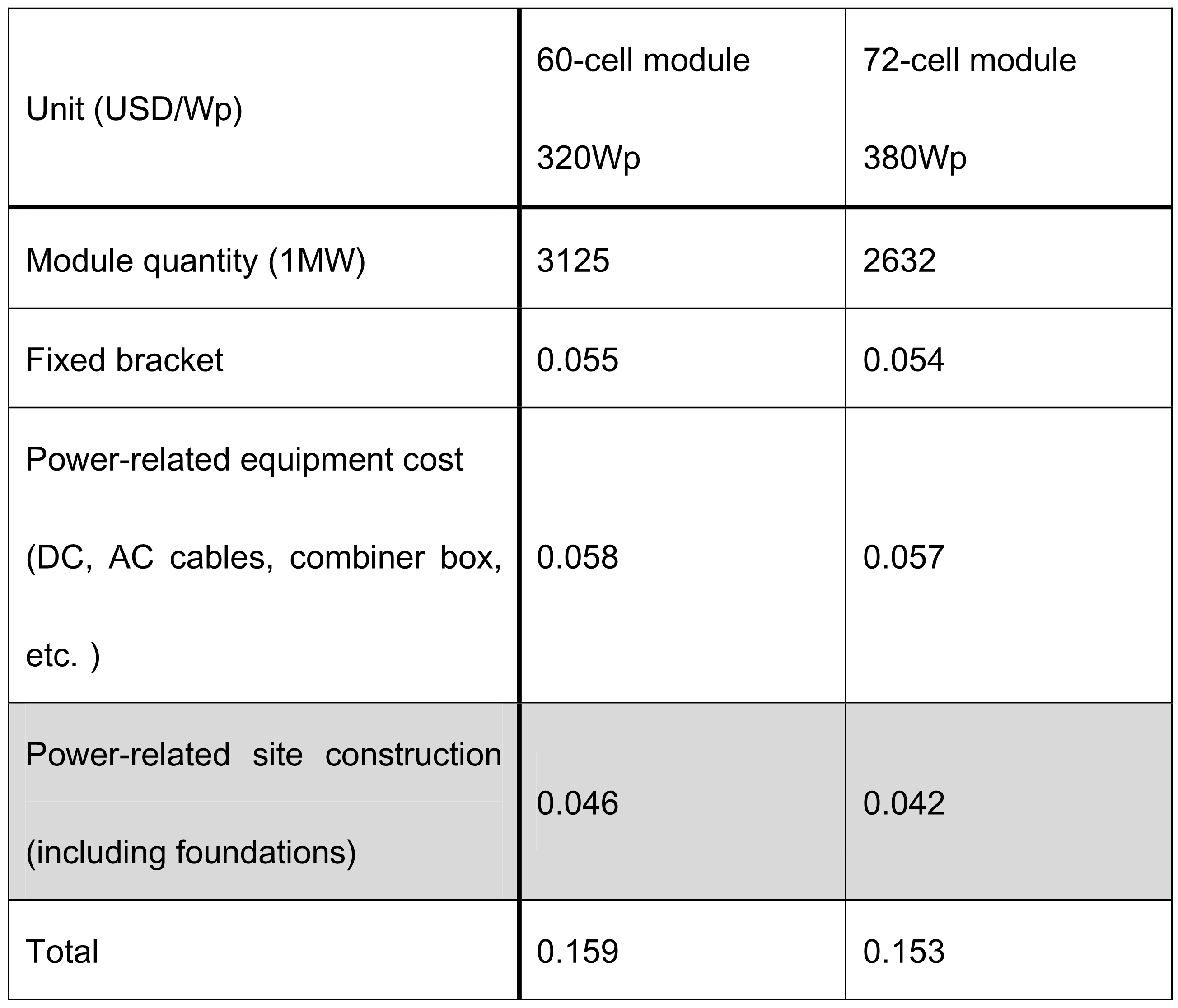
3.Comparison between larger silicon wafer (166mm) module and existing module
The size of module began to increase again in 2018 with two options: increasing the number of cells, or increasing the size of wafer. The number of cells can be increased from 72 to 78 (+8.3%) and the size of wafer can be increased to M4 (side length 161.7mm,+5.7%) or even 166mm (approximate +12%). The change from 60-cell to 72-cell shows that the increase in the number of cells can reduce the number of strings, but has limitation on the savings in bracket and pile foundation, while increase in the size of wafer is more beneficial to the reduction in BOS costs. Thus, the size of wafer shall be increased as much as possible as long as the production can be realized and the module installation has no obvious difficulties. The following table shows detail calculation of system costs using 166mm wafer:
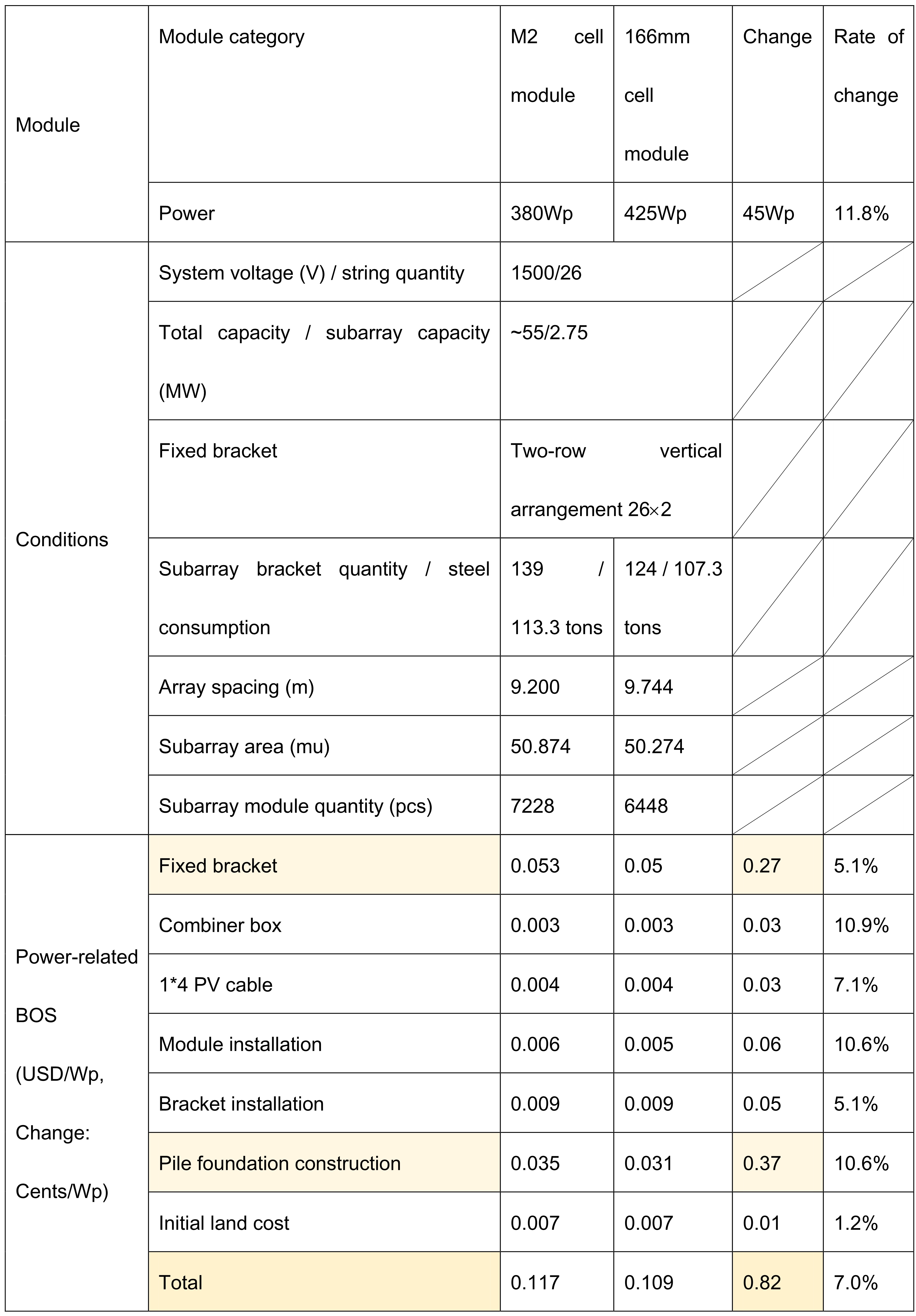
Obviously, when the power is increased by 11.8%, the BOS costs can be saved by USD 0.008/Wp, and the largest savings are of pile foundation and bracket. The above calculation is based on the lower-cost structure in China, and the BOS cost savings will be even higher if tracker is used or in area with higher labor and land costs.
Summary
The BOS cost savings of photovoltaic power stations resulted from the improvement of module efficiency are well known in the industry, and the savings can be calculated in a concise way. The increase of module size can also result BOS cost savings. This paper reviews the BOS cost savings caused by the change of cell size from 125mm to 156mm and the change of cell quantity from 60 to 72, furthermore clarifies that cells can be made even bigger to save BOS costs. The detail calculation shows that using 166mm monocrystalline cell can save BOS costs by USD 0.008/Wp compared with the 156(.75mm) cell, and is an ideal choice in today’s high competition market with significantly growing pressure on cost.